回转窑内频繁结大蛋的原因及解决方法
发表日期: 2020-08-19 文章来源:郑矿机器 作者:
结蛋的主要成因有以下几点:
首先有害成分是预分解窑内结蛋的原因之一 。根据国内外一些预分解结皮结蛋样的分析得知,有害成分(主要是K2O、Na2O、SO3)是影响结皮结蛋的重要原因,结皮料有害成分的含量明显高于相应生料中的含量,有害成分能促进中间相特征矿物的形成,而中间相是形成结皮结蛋的特征矿物(如钙明矾石2CaSO4·K2SO4,硅方解石2C2S·CaSO4等)。原燃料中的有害成分在烧成带高温下挥发,并随窑气向窑尾移动,造成并促进窑后结蛋特征矿物的形成。在物料向窑头运动的过程中,随着窑内温度与气氛的变化,特征矿物分解转变,其中的有害成分又被释放出来。进入高温带后绝大部分又挥发出来,形成内循环,使有害成分在窑系统中不断富集。有害成分含量越高,挥发率越高,富集程度越高,内循环量波动的上极值越大,则特征矿物的生成机会越多,窑内出现结蛋的可能性越大。
其次从配料上看,液向量及其性质的波动大,体现在熟料的三率值上主要是熟料的铝率波动大。传统的理论认为:配料方案中A1203、Fe203含量高,SiO2含量低是形成窑内结蛋的前提条件之一。所以国内外绝大多数预分解窑都控制A1203,+Fe203<9%,液相量24%左右,Si02>22%,n>2.50。且多余的mgo相当于“提铁”,实质上导致熟料的烧成范围变窄,液相提前出现,表面张力减小,黏度降低,易长厚窑皮和结蛋。接大蛋和熟料n、p的高低没有太直接的关系,重要的是液相的性质。当液相量极其黏度发生较大的变化时,操作与料不同步,就可能导致出大蛋,也就是说熟料液相性质的变化是诱导结蛋的因素之一。
再次是操作上的影响。①由于种种原因,四班操作不统一,窑况不稳定,造成煤粉滞后燃烧。煤粉的滞后燃烧使物料在过度带液向量增多,当液相含量达到物料总量的12%~17%时,就比较容易烧成小的物料球,升温速率越小,时间越长,就容易形成大蛋。②窑前喂煤量偏大,煤粉无法在窑前充分燃烧;③窑前温度低,煤粉无法获得足够的热量,一次风用量不当,对二次风的引射能力不够,使煤粉燃烧滞后;④内外风配合不当,外风大,内风小,并且当煤粉灰分波动时,不能正确调整内外风以保持煤粉及时燃烧。
*后是窑内结圈的影响。俗话说“十圈九蛋”也就是说当形成蛋的前提条件具备后,正是圈的存在进一步加剧了蛋的形成。不难理解当物料受到圈的阻挡,并在此不断滚动,一方面由于对小球核的挤压,使液相存在于球核表面,另一方面,由于上述原因,在此存在一定液相,使小球不断黏结物料并不断滚动逐渐形成大蛋。当蛋大到一定程度,受到物料冲击和挤压作用,大蛋跨过圈从窑内滚出来。有时烧成带前端窑皮偏厚形成台阶时,也会在此形成大蛋。
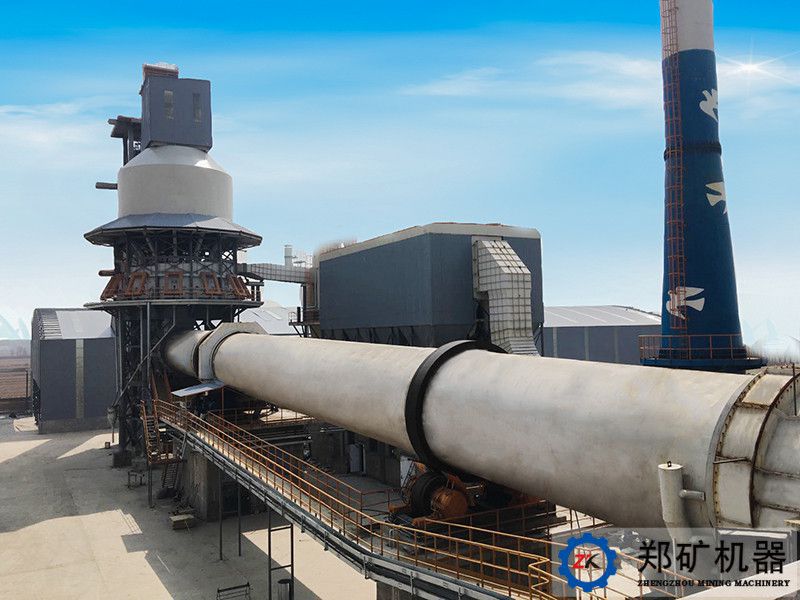
针对以上成因,解决措施主要有:
①选用品位高,有害成分少的原燃料。
②选用合理的率KH=0.95+_0.1,SM=2.5+_0.1,IM=1.5+_0.1,加强均化,保持入窑生料成分的稳定;
③规范操作,优化工艺操作参数,不断积累经验,根据不同来料和燃料及时调整操作方法,适时调整内外风比例,开大内旋风,同时减少头煤0.1~0.3t/h,以保证煤粉在窑前完全燃烧;
④尽量避免窑内结圈,从而防止窑内结大蛋。当窑内结圈要及时处理掉,结后圈可以通过冷热交替法,结前圈可以通过调整火焰形状把圈烧掉。
- 下一篇: 水泥磨工序电耗高的原因分析
- 上一篇: 球磨机的突出优势